Divya Washing Machine
Shaped by the people who use it.
The world’s first flat-packable manual washing machine.
Designed for the day-to-day family life of women and girls in remote and displaced communities, the Divya Washing Machine has enough capacity to meet the laundry needs of a large family.
It’s simplified design reduces the need for repairs. It can be easily dissembled allowing the machine to be fixed with off the shelf components or, locally available skills and tools. Built with commercial-grade components and stainless-steel construction, it has greater potential to be recycled at the end of its life.
It has a 30 minute wash cycle, with only a few minutes of manual turning - saving up to 75% of time for it’s user, and halves water consumption.
The next generation of the Divya washing machine has been shaped by the people who use it.
Every iteration is a result of listening to our users feedback, gathering data and caring deeply about making design changes that have tangible impacts on the daily lives of our users.
Through conversations in peoples homes, community centres, refugee contexts, hospitals and other contexts - we’ve taken user feedback and turned it into practical, meaningful improvements.
Built-in Scrubber: Textured lid surface helping to remove tougher stains.
One of the most requested features was a built-in scrubber, now seamlessly integrated into the lid. In many of the places where Divya is used, people rely on brushes or rough surfaces to tackle tough stains on collars and cuffs before washing their clothes. Now, instead of needing a separate tool, users can simply lift the lid and scrub stains straight away, making the washing process smoother and more efficient.
Wider Lid: Increased opening for washing larger fabrics like duvets and blankets.
We’ve also made accessing the drum easier by widening the lid opening. In past iterations, the machine was primarily designed for everyday clothing, but we quickly learned that users want to wash larger household items like blankets, towels, and even duvets. A larger opening makes it easier to load and unload these bulkier fabrics, ensuring that Divya meets the real needs of the people using it.
Faster Drain: New tap design reduced drainage time by 50%.
Saving time is at the heart of each improvement, which is why we've redesigned the tap for faster water drainage. Previously, a significant portion of wash time was spent waiting for water to flow out of the drum. Now, with a large tap, drainage is quicker, cutting down wash cycles and allowing more people to use the machine in communal settings each day. These taps are also widely available to purchase within the countries we distribute machines, meaning that if they break - a new one can just be fitted very easily.
Stronger Wheels: More durable wheels for greater mobility across each environment.
Stronger, more durable wheels mean the machine can go wherever it’s needed. Whether moving between homes, across courtyards, or over moderate terrain, the upgraded wheels provide smoother transportation. In many communities, families share a single machine, rolling it from house to house. In other communities the machine is used for income-generation, and can be wheeled from home to home washing clothes for a community. This improvement ensures Divya is built to last, no matter how far it travels.
Each adjustment has been developed through a deep care and understanding of what users want.
Laura - R&D Lead
‘My number one favourite feature on the machine is the scrub door feature. We learnt from users that they were struggling to clean tough stains, such as tough stains on their cuffs or collars.
We had a fantastic co-creation session in India April 2024 we learnt that they were using brushes and scrub surfaces to get those tough stains out before and after putting them in the machine.
What we've done is integrate that into the machine itself. During the wash cycle you can take the clothes out, identify those tough stains, you've got a surface immediately available. You can then put them back in the wash and continue the cycle.'
Jack - R&D Lead
'The use cases we looked at were in schools and communities where there was lots of use of the washing machine. Taking 6 minutes per wash was taking too long, so a dramatic design change was needed for the tap.
It's a standard tap fitting, that's really common and widely available to purchase in the contexts we work, should a replacement be necessary.
The most important thing is reducing the drain time to just 3 minutes, so if you're in a communal setting, and you’re waiting to wash your clothes, you can now use the machine almost immediately after the last use.'
Vicky - Design Engineer
After having feedback on the wheels, both the material they were made of and the surfaces they are running on, it was clear we needed a change.
We got lots of different materials from suppliers, took them up to Ashton court in Bristol. We tested how it felt, how much they wore - some of them wore down a lot!
People are using the wheels a lot more than we thought, so it's about making them robust for being able to transport them, not needing surfaces very often. We want to avoid servicing and make the wheels last as long as possible.
Hélène - Design Engineer
One of the things we kept hearing from users, again and again, was how hard it is to wash big things like bedsheets and blankets.
They’re bulky, they get super heavy when wet, so trying to get them in and out through a small opening is a struggle. This made us look into design and how we can improve that with Divya and realised that something as simple as the size of the opening actually can actually make a difference.
So we made it bigger. It might not seem like a dramatic change at first, but for the people using it every day, it makes the whole experience smoother, easier, and way more manageable. And that really matters.
The Evolution of the
Divya Washing Machine
The Salad Spinner (2018)
Having spent a year in India designing improved cookstoves for rural communities, Nav returned to the UK with a promise to help his neighbour, Divya, who spent hours every week handwashing her family's clothes. This promise became the seed of The Washing Machine Project.
Nav gathered friends around a table and posed the question: What is a washing machine, really?
They broke it down to its core components; agitation, detergent, and time, and realised that even a basic household item like a salad spinner could offer all three. They took off their socks and began testing the theory, washing clothes in the spinner. It worked.
They never used it for food again.
Divya 1 — The First Prototype (2019)
In March 2019, we took the first-ever Divya prototype, crafted from a repurposed chemical drum, to Iraq to speak directly with displaced families about their laundry routines. Their input validated the urgent need for a manual solution.
Shortly after, Oxfam committed to purchasing 50 machines. Prototyping began in earnest between July and November 2019, with field research trips to both Iraq and the Philippines to guide the development. By December, the team was hand-building 50 Divya 1 machines in a maker space in Wembley, which were shipped and distributed to Jeddah 1 Camp in Iraq in early 2020.
This version was rugged and experimental. A proof of concept that helped TWMP understand how people interacted with the machine in real-life settings. It paved the way for improvements based on user feedback.
Divya 1.5 — Co-designed and Community Built (2021)
Building on learnings from the field, The Washing Machine Project began developing Divya 1.5 in 2021 and was a significant redesign. This version marked the start of a collaboration with RS Group, who supplied engineering support and materials.
Made largely from plastic, with a wooden stand, the machine had a gearbox that not only aided washing but also gave the machine a spin cycle.
Between June and August 2021, 32 Divya machines were built in Newport by RS volunteers.
In September, the team returned to Iraq to distribute the machines to Mamrasham Camp, where Care International Iraq had procured 30 units.
Although a massive step forward, we started learning that heavy, plastic machines delivered to remote communities highlighted the challenges of sustainability and repairability in such contexts. A redesign was in order.
Divya 1.65 — Designed for Scale and Sustainability (2022–2025)
The latest version, Divya 1.65, is the result of three years of iterative research, testing, and engineering refinement. It represents a complete rethinking of traditional washing machine design; optimised for simplicity, local assembly, and end-of-life reuse.
Drawing from experiences in Uganda, where transporting large plastic machines to remote islands proved unsustainable, the team developed a flat-packable version that can be assembled anywhere with basic tools like Allen keys and spanners.
Key innovations include:
Foldable metal tabs instead of industrial crimping
Thinner metal sheets that can be hand-rolled into shape
A door placed above the waterline to eliminate gasket leaks
Elimination of the gearbox to reduce failure points
An intentional "underengineered" approach to boost durability and longevity
At end of life, the machine can be disassembled into recyclable and reusable metal parts — adaptable for welding, bending, or other community uses without requiring industrial recycling infrastructure.
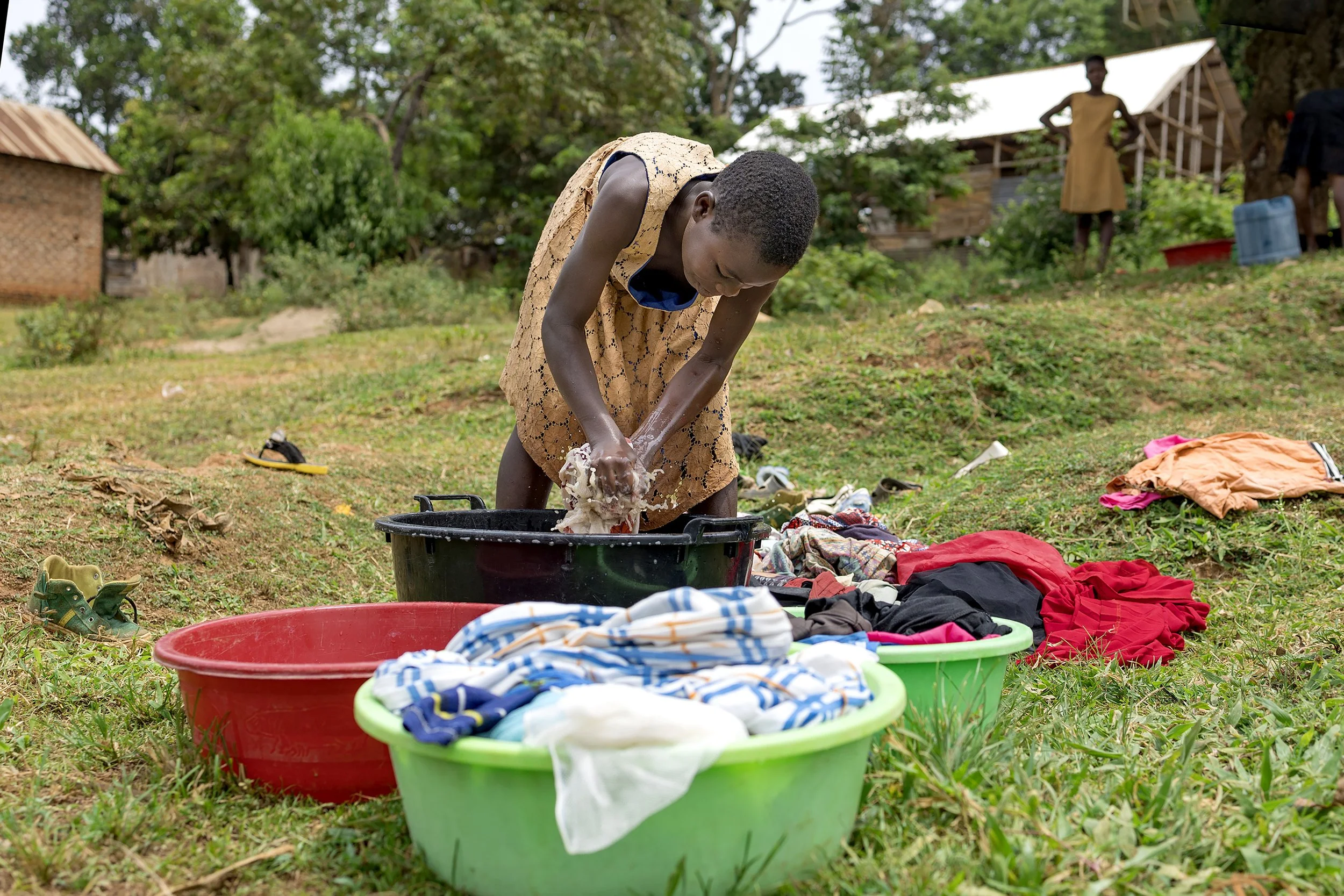
Help The Washing Machine Project reach more users.
Donate to TWMP Foundation
TWMP Foundation is a registered UK charity providing funding, oversight, and governance to support The Washing Machine Project’s work.
While the CIC designs and delivers practical solutions like manual washing machines, the Foundation independently reviews and funds eligible charitable projects aligned with our shared mission.
Learn more here: https://www.twmpfoundation.org/